proexcellency
Sap QM Online Training
SAP Quality Management is a part of SAP R/3 system and is integrated with other SAP modules like SAP Material Management (MM), Production Planning (PP), and Plant Maintenance (PM). QM is an integral part of logistic management and it is used to perform quality functions such as quality planning, quality assurance, and quality control, at various stages such as incoming material stage, in-process manufacturing process stage, and after production as well.
ProExcellency Bangalore is the top choice for SAP QM Online Training because of their highly experienced educators, practical approach, and industry-focused curriculum. We ensure that students master SAP QM ideas as well as actual application skills, while also providing real-time access to SAP systems, interactive learning, and customizable training schedules. ProExcellency provides a full learning experience to assist professionals thrive in the competitive job market with economical pricing, certification guidance, and committed support, making it the ideal choice for SAP training in Bangalore.
Introduction to SAP QM online training:-
The module called SAP Quality Management is very significant in the implementation of an SAP ERP system. Its general purpose is ensuring that a company maintains the level of quality over the products as well as their processes which they manufacture. This module integrates itself effortlessly with the following modules like MM, PP, and SD which ensure the complete quality check during procurement to its manufacture and till sales.
The professionals will get knowledge on the aspects of planning, inspection, notifications, and audit management using our online SAP QM training. The course will ensure hands-on training with real case studies, professional support for anyone-whether an entry-level professional or a seasoned SAP consultant aiming to develop special expertise in QM-from our team to teach SAP QM features to you as effectively as possible.
Overview of Quality Management in SAP :-
SAP Quality Management is a sophisticated module that helps organizations maintain quality standards throughout their operations. It provides comprehensive support for quality planning, inspection, and control, ensuring compliance with industry standards and customer expectations.
SAP QM Key Features
-
Quality Planning: Inspection methods, sampling processes, and quality control parameters can all be specified.
-
Quality inspection includes incoming, in-process, and final inspections to verify product quality.
-
Quality Notifications: Defects, deviations, and customer complaints are tracked and managed.
-
Quality Control: Statistical process control and corrective action to ensure manufacturing quality.
-
Audit Management: Conducting internal and external audits to ensure compliance with regulatory standards.
-
Integration with other SAP modules: Work seamlessly with the MM (Materials Management), PP (Production Planning), and SD (Sales & Distribution) modules to ensure end-to-end quality.
Organizations can use SAP QM to eliminate defects, improve product quality, and optimize their manufacturing processes. For these reasons, the manufacturing, pharmaceutical, automotive, and consumer products industries require such a critical module.
Master data in SAP QM:-
Master data in SAP Quality Management (QM) serves as the foundation for quality activities like inspections, quality notifications, and audits. Predefined data that remains constant across multiple transactions and procedures.
Master data components in SAP QM
1. Material Master
It contains material-specific quality details.
Specifies the sorts of inspections (such as goods reception, in-process, and final inspection).
Maintains quality-related parameters, such as inspection setup and control indications.
2. Inspection plans
Tell me what to look for in a substance.
Describe its characteristic, testing apparatus, and specifications.
Determine the sampling and inspection methodologies.
3. Master Inspection Characteristics (MICs).
Parameters to be inspected, such as the dimensions, weight, or chemical composition
Could either be quantitative length and weight.
4. Sampling procedures
Calculate the number of units in a batch to inspect.
Justify fixed sample sizes and percentage-based sampling.
5. Catalogs and Code Groups.
Predefined codes are used to record problems, use decisions, and results.
Simple to classify errors, determine causes, and take corrective action.
6. Quality Information Records These documents contain supplier-related tender quality agreements.
Only authorized vendors will be allowed to deliver the materials.
7. Test Equipment The master controls the measuring tools used for inspections.
Keeps track of calibration and maintenance schedules.
Master data in SAP QM ensures consistency, precision, and efficiency in the quality management process, resulting in higher-quality goods and greater compliance.
Quality Notifications in SAP QM
Quality Notifications (QN) in SAP QM are used to record and handle faults, complaints, and non-conformities in products or processes. They assist in tracking quality concerns, identifying root reasons, and implementing corrective actions to raise quality standards.
Quality Notifications in SAP QM
Customer Complaint (Q1):
-
Addresses product quality problems.
-
Helps to document the problem and initiate corrective steps.
Internal Problem Notification (Quarter 2)
-
Used to document quality issues discovered within the organization, such as manufacturing flaws and equipment breakdowns.
-
It facilitates internal defect investigation and process improvement.
Supplier Complaint (Quarter 3).
-
It is used to report quality issues with items provided by vendors.
-
It guarantees that providers take corrective actions to maintain quality requirements.
Key Benefits of Quality Notifications:-
-
Defect recording: Keep track of and classify quality flaws such as incorrect dimensions or surface flaws.
-
Cause analysis: Use predefined codes to find the underlying causes.
Action management entails specifying corrective and preventive measures to address quality issues.
-
Integration with Other Modules: Interfaces with SAP MM, PP, and SD to ensure a smooth quality management process.
-
Workflow & Approvals: Issues are addressed methodically through approvals and escalations.
-
Quality issues are tracked and reported using sophisticated analytics to drive continual improvement.
Quality Notification Process Flow:-
1. Quality Notification: Fill in all issue details, affected materials, and defect codes.
2. Review and analyze - Determine root cause and assign responsibilities.
3) Define Corrective Actions to resolve and prevent future issues.
4. Monitor and Close notice: Verify effectiveness of activities and close notice.
SAP QM Quality Notifications enable the organization to manage its quality issues, reduce faults, and boost customer happiness.
Quality certificates in SAP QM:-
In SAP QM, Quality Certificates (QCs) are official documents that attest that a product meets the required quality criteria. They are typically given to consumers or suppliers and serve as verification that materials or completed goods exceed predetermined quality standards.
Key Features of Quality Certificates in SAP Quality Management :-
-
Certificate Profiles - Determine the format, structure, and content of the quality certificate.
-
Inspection Results Inclusion - Automatically retrieve inspection results from quality checks.
-
Certificate Output Management - Create, print, or send high-quality certificates online.
-
Integration With Other SAP Modules - Coordinates with Materials Management (MM), Sales and Distribution (SD), and Production Planning (PP) to ensure seamless quality control.
Different types of quality certificates
-
A Certificate of Analysis (COA) certifies that a product meets specific chemical, physical, or microbiological requirements.
-
The Certificate of Conformance (COC) indicates that a product meets the specifications of a customer or a regulatory agency.
-
Inspection Certificate (based on ISO 10474 / EN 10204): standardized certificates for international trade and compliance.
Procedure for Creating a Quality Certificate in SAP QM:-
-
Define Certificate Profile: Indicates the necessary content, format, and inspection information.
-
Attach the certificate profile to materials/customers. Connect the certificate profile to the relevant material or client master data.
-
Quality Inspection includes gathering test findings from inbound, in-process, and final inspections.
-
Quality Certificate Creation - Use SAP transaction codes QC21 for Manual Certificate and QC22 for Automatic Certificate.
-
Certificate Output - Print or email the recipient.
Advantages of Using Quality Certificates in SAP QM :-
-
Ensures compliance: Quality meets industry norms and customer expectations.
-
Increase customer confidence by providing information about the product.
-
Improve documentation quality while reducing manual effort and errors.
-
Improve customer and supplier relationships by streamlining transactions and increasing quality consciousness.
Benefits of adopting SAP QM Quality Certificate include improved product reliability and company performance.
Conclusion :-
Quality management is a critical job in SAP that ensures product quality, regulatory compliance, and customer happiness. QM, which is seamlessly connected with other SAP modules, helps firms simplify quality inspections, manage faults, track quality notifications, and generate quality certificates.
Businesses can reduce defects, improve process efficiency, and uphold high standards of quality in production, sales, and procurement by utilizing SAP QM's features, which include quality planning, inspection, defect management, audit control, and reporting.
ProExcellency's SAP QM Online Training provides professionals with in-depth knowledge, hands-on experience, and real-world case studies to grasp SAP's quality management processes. Whether you wish to update your abilities or prepare for the SAP QM certification,
Q&A for SAP QM Online Training: -
1. What is SAP Quality Management (QM), and why is it important?
A: SAP QM is a module of SAP ERP that deals and improves the quality of materials, products, and processes within an organization. This module is the most important since it ensures quality in products, industry standards, and customer satisfaction. Companies may use SAP QM to check the quality, monitor defects, manage supplier quality, and obtain quality certificates; all these processes reduce defects, efficiency, and maintaining high standards.
2. What are SAP QM online training pre-requisites?
A: Any pre-requisite to get into SAP QM Online Training is not mentioned; however, basic awareness of business process, manufacturing concepts, and related quality management would serve as a perfect pre-requisite. Know-how regarding SAP ERP or other SAP modules like MM, Materials Management and PP, Production Planning would always be an advantage but is certainly not a condition. This class is open both to fresh candidates and experienced users who wish to enhance their ability in SAP's quality management systems.
3. What structure does SAP QM online training take?
A: Our SAP QM Online Training is designed to provide comprehensive and hands-on learning. The course consists of interactive instructor-led seminars, hands-on practice, and real-time case studies. Quality planning, inspection methods, quality notices, audit management, and preparation for certification are key subjects covered. Flexible learning options will enable you to learn at your own pace with constant support from instructors for ensuring successful completion.
Duration
Duration
30-35 hrs
Shipping & Returns
Shipping & Returns
Dimensions
Dimensions
Care Instructions
Care Instructions
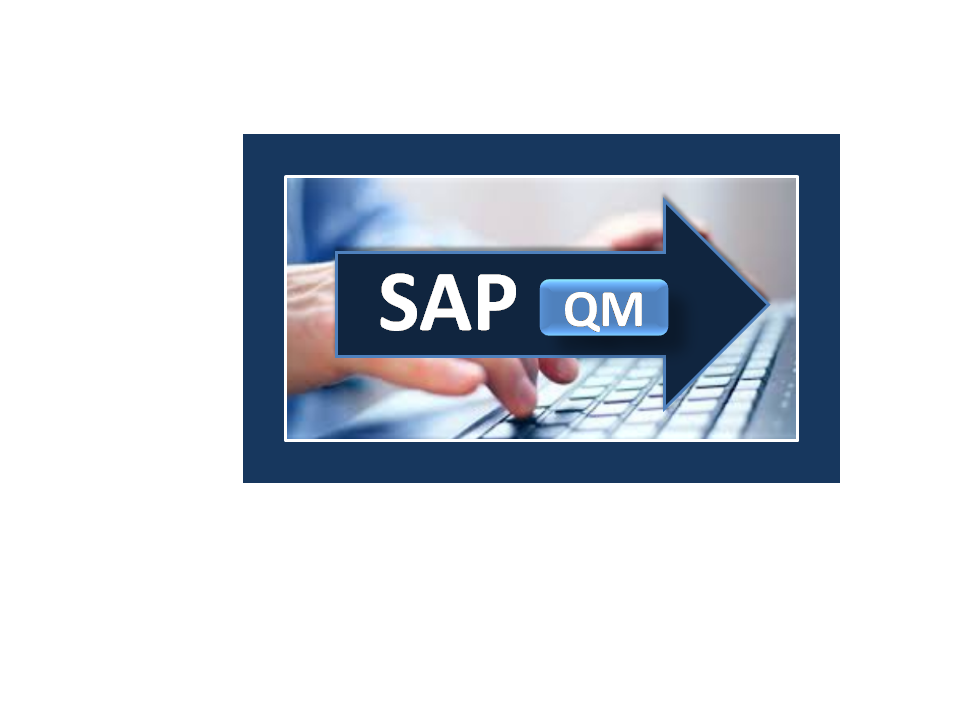